"Flexible" electronic skins or smart wearable devices have attracted more and more attention due to their wide application in medical healthcare monitoring, intelligent robots, and intelligent prostheses. Electronic skin can quickly detect the small pressure changes or movement postures of one human body and convert these mechanical signals into electronic signals at the human-machine interface, which is also essential in today's cutting-edge research.
Most electronic skin sensors, such as resistance, capacitance, and temperature sensors, require external or additional electric energy to supply power. Recently, some researchers have used the boelectricity phenomenon to power electronic skin sensors. However, in comparison with the boelectricity phenomenon, flexible piezoelectric polymers exhibit the features of higher power density, high force-electric sensitivity, and better operation stability; therefore, they are more suitable for self-powered sensors application in wearable devices.
The most used materials for manufacturing flexible piezoelectric devices are PVDF (polyvinylidene fluoride) and its copolymer PVDF-TrFE with high β-phase content, as well as their composites with piezoelectric ceramic particles. PVDF polymer or its copolymer has low dielectric constant, low acoustic impedance, excellent thermoelectric and ferroelectric properties, and it can be processed into any shape. These properties make it more suitable for flexible self-powered electronic skin applications. However, compared with "hard" inorganic piezoelectric ceramics or single crystals, the piezoelectric properties of PVDF polymers or their copolymers are still very limited.
In this work, Prof. Shuxiang Dong’s group reported a 3D-printed PVDF-TrFE piezoelectric film (PF) coated with one pair of a dislocated interdigital electrode (ID) to produce multiple, alternatively tilt-polarized regions in the cross-sectional area. Experimental results showed that the tilt-polarized PF exhibits more than ten-fold higher sensitivity, in terms of volts/kPa, than a conventional PF, which has been applied an invention patent recently.
The theoretical analysis further reveals that the enhanced piezoelectric effect of the film can be attributed to the larger electric dipole moment due to tilt dipole orientation in PVDF-TrFE polymer. The experimental measurements show that the ID tilt-polarized PVDF-TrFE film (ID-TPPF) can produce a stable peak voltage of 73.5 V under dynamic compression stress of 50 kPa at 1 Hz, corresponding to a pressure sensitivity of 1.47 V/kPa, which are 14.7 times and 3.6 times those of a PVDF-TrFE film with conventional thickness-polarization (CTPPF) and in-plane polarization (ID-IPPF), respectively.
Correspondingly, the peak power density of ID-TPPF is as high as 478 μW/cm2, while at a load of 3 MΩ, the load power is still 207 μW/cm2, which even instantly lights up eight LEDs connected in series without using any charging capacitor.
This work confirms that the 3D-printed ID-TPPF shows excellent potential in self-powered tactile sensors and artificial skin applications in the future.
The related research was published in the journal Nano Energy on March 17, 2021, entitled “A 3D-printed, alternatively tilt-polarized PVDF-TrFE polymer with enhanced piezoelectric effect for self-powered sensor application.” (DOI:10.1016/j.nanoen.2021.105985).
The first author of this paper is the Ph.D. candidate, Xiaoting Yuan (2017), and ProfessorShuxiang Dongis the corresponding author of the paper. The work was jointly supported by the National Natural Science Foundation of China (51772005,51132001), Project 863, and Beijing Key Laboratory of Magnetoelectric Functional Materials and Devices.
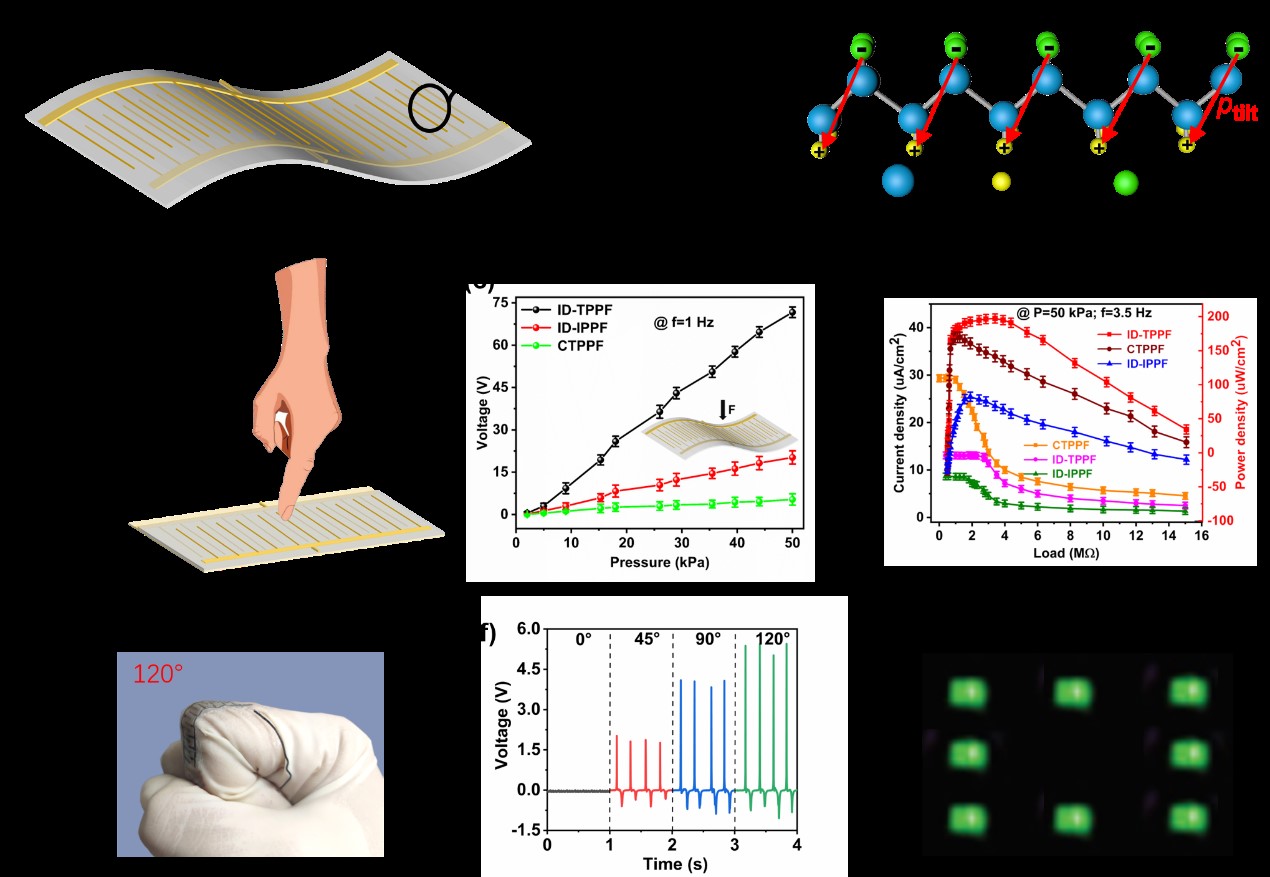
(a) Schematic diagram of theID-TPPF. (b) TheID-TPPFwas tapped. (c) Output voltage as a function of the dynamic compressive force of the ID-TPPF,ID-IPPF, and CTPPF. (d) Current density and load power density as a function of load resistance of the ID-TPPF,ID-IPPF, and CTPPF. Photo of ID-TPPF is installed on the wrist joint and bends at 120° (e) and output voltage (f). (g) 8 LEDs were lighted directly when the finger lightly pressed the ID-TPPF.