Piezoelectric materials realizing the conversion between mechanical energy and electrical energy are widely used in integrated piezoelectric microsystems. Among them, lead zirconate titanate (PZT) based ceramics and the latest potassium sodium niobate (KNN) based lead-free piezoelectric ceramics show excellent piezoelectric performances. but they have encountered many difficulties in the fabrication and application of flexible electronic devices due to their brittleness character and easy to break. It is also difficult to integrate PZT ceramics into Si-based microsystems because of the excessively high-temperature preparation required. In this case, organic polymer polyvinylidene fluoride (PVDF) material is more attractive. Traditionally, to obtain the piezoelectricity, first, a uniaxial stretching is necessary to transform α-phase into β-phase in PVDF polymer; and second, a strong electric field as high as 105 V/mm (in high-risk coefficient) is necessary to align the randomly oriented molecular dipoles along the applied field direction in the PVDF polymer for producing a macroscopic piezoelectric effect. Although the PVDF’s co-polymer (PVDF-TrFE) features a high content of β phase without experiencing a uniaxial stretching, the electric poling process is still necessary to produce effective piezoelectricity, but high-voltage or high-field brings the risk of electric breakdown. Similarly, the piezoelectric PVDF prepared by electrospinning does not require uniaxial stretching, but a higher electrostatic field is also necessary. Piezoelectric microelectronic devices also strongly depend on the preparation method. Currently, the manufacture of piezoelectric polymer and devices still largely relies on conventional tape casting fabrication techniques, resulting in excessive post-process and limited dimensional design problems.
Recently, Prof. Shuxiang Dong’s group reported a poling-free PVDF polymer nanocomposite via mechanically directional stress field. It is found that the mechanical orientation stress field can induce the PVDF copolymer to transform from disordered, star-shaped nanocrystals to ordered, self-polarized fiber chain nanocrystals. Without any high voltage polarization, the obtained piezoelectric and electromechanical coupling properties are comparable to those of the traditional, high-voltage poled PVDF polymer. Furthermore, a 7-layer series-connected, self-powered circular pressure sensor was fabricated using multi-material 3D-printing technology for a self-powered pressure sensor array. The fabricated sensor exhibits a high sensitivity of 235 mV/kPa and a high-power density of 0.9 mW/cm2 under dynamic pressure, and it is nearly 8 times higher than that of a conventional, poled single-layer PVDF sensor. Finally, a (3 × 3) real-time lighting tactile sensor array is fabricated via 3D printing method, confirming its feasibility for practical application.
The related research was published in the journal of Nano Energy, entitled “A poling-free PVDF nanocomposite via mechanically directional stress field for self-powered pressure sensor application” (DOI: 10.1016/j.nanoen.2022.107340). The first author of this paper is the Ph.D. candidate, Yuan Xiaoting (2017), and Professor Dong Shuxiang is the corresponding author of the paper.
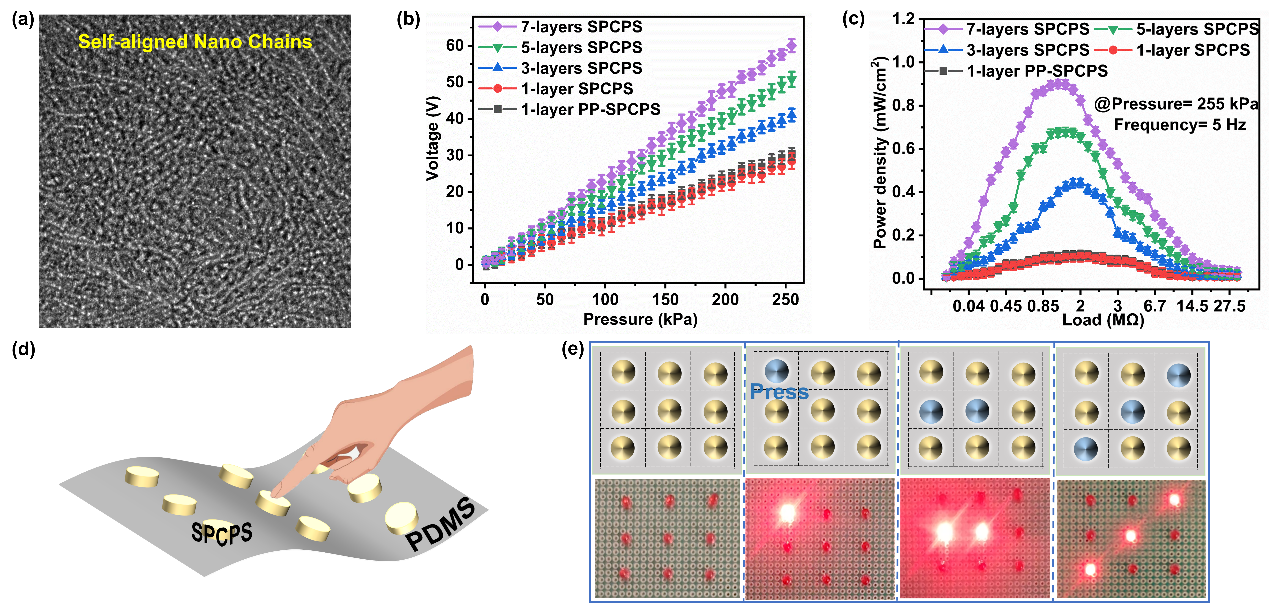
(a) Ordered chain nanofibers;(b) Relationship between output voltage and pressure of self-powered circular pressure sensor;(c) Relationship between power density and load resistance of self-powered circular pressure sensors;(d) Schematic of (3×3) real-time light-emitting tactile sensor array;(e) Photo of the corresponding LED light on when the corresponding tactile sensor is pressed